机电设备数字化化生产全流程控制
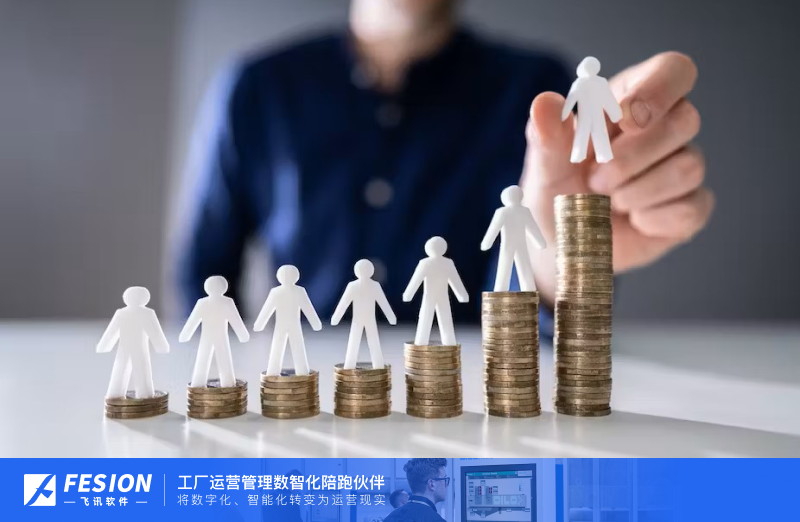
机电设备数字化化生产全流程控制:实现智能制造的崛起
随着信息技术的快速发展和工业互联网的兴起,机电设备数字化化生产全流程控制已成为现代制造业的重要趋势。数字化化生产全流程控制可以使企业实现高效、灵活、精确的生产运作,提升产品质量、提高生产效率,推动智能制造的快速崛起。
一、数字化化生产全流程控制的概念与意义
所谓数字化化生产全流程控制,是指利用现代信息技术来实现对机电设备生产全过程进行全方位、全程度的监测、控制和优化的管理方式。它将传统的手工操作逐步替代为计算机控制和自动化系统,通过数据采集、传输、分析和处理,实现全流程的精细化管理和智能化决策。
数字化化生产全流程控制具有以下几个方面的重要意义:
1. 提高生产效率:通过数字化化生产全流程控制,可以将原本繁琐的人工操作转变为全自动或半自动的生产方式,提高设备运行效率和生产速度,减少人为错误和生产线停机时间,从而大幅提高生产效率。
2. 提升产品质量:数字化化生产全流程控制能够实现对每一个工艺环节的精确监测和控制,确保产品在每个生产环节中的质量和一致性。通过实时数据分析和预警系统,可以及时发现问题并进行调整,提高产品的合格率和稳定性。
3. 降低成本费用:数字化化生产全流程控制可以实现对生产资源的合理配置和利用,避免资源的浪费和过度投入。同时,通过实时监测和优化,可以减少能源消耗和废品产生,降低生产成本,提高企业的竞争力。
4. 强化安全管理:数字化化生产全流程控制可以实现对设备运行状态的实时监测和预警,减少人员因操作失误或设备故障造成的事故风险。同时,通过远程监控和控制技术,可以减少工人接触危险环境的机会,提高安全性。
二、数字化化生产全流程控制的实施步骤与关键技术
实施数字化化生产全流程控制需要经过以下步骤:
1. 前期准备:明确数字化化生产全流程控制的目标与需求,制定详细的实施计划,并确保企业内部各相关部门的理解和支持。
2. 数据采集与传输:通过传感器、网络等技术手段,对设备运行状态、工艺参数、质量指标等关键数据进行实时采集,并将其传输到数据中心或云平台。
3. 数据处理与分析:利用数据分析软件和算法,对采集到的数据进行处理、清洗和分析,提取有用的信息和规律,并通过可视化界面展示给相关人员。
4. 监测与控制:根据数据分析结果,实现对设备运行状态、工艺参数等关键要素的实时监测和控制。通过远程操作或自动化系统,进行设备的远程开关、调整和优化。
5. 优化与改进:通过不断积累和分析数据,对生产流程进行持续优化和改进,提高生产效率和产品质量,并根据市场需求和技术进步,不断更新和升级数字化化生产全流程控制系统。
在数字化化生产全流程控制的实施过程中,有一些关键技术起到了重要的作用:
1. 传感器技术:用于实时采集设备和生产过程中的各项数据。
2. 云计算与大数据技术:用于存储和处理海量的数据,并提供强大的计算能力和分析工具。
3. 人工智能与机器学习技术:通过对数据的分析和模式识别,实现对生产流程的预测、控制和优化。
4. 工业物联网技术:用于设备之间的互联互通和信息共享,实现设备之间的协同工作和整体调度。
三、数字化化生产全流程控制的前景与挑战
数字化化生产全流程控制具有广阔的前景和巨大的潜力。随着工业互联网的不断发展,数字化化生产全流程控制将成为推动智能制造的核心技术和关键手段。它将促进企业向产业链价值链的高端延伸,提高产品附加值和市场竞争力。
然而,在实施数字化化生产全流程控制时,也存在一些挑战需要克服。首先是技术挑战,包括数据采集与传输的安全性、数据处理与分析的复杂性等。其次是组织与管理挑战,包括培训员工的技术水平、打破部门壁垒的协同合作等。
总之,数字化化生产全流程控制是实现智能制造的重要途径,它将推动机电设备制造业向高效、智能、可持续的方向发展。企业应积极抓住机遇,加强技术创新和人才培养,不断完善数字化化生产全流程控制系统,提升自身竞争力,实现可持续发展。
飞讯软件成立于2006年,拥有自主研发低码开发平台。是一家集“营销、制造、采购”全链路数智化工厂定制方案商和服务商。产品服务:数字化车间、互联工厂和链主工厂。公司以MRO、ERP、MES、WMS、CRM、SRM等产品为基础,为客户提供数智化工厂整体方案规划和落地陪跑服务,服务范围覆盖珠三角和长三角地区。致力于帮助客户创立切合实际场景、可传承、可创新的数字化运营体系,解决“流程信息化、管理数字化和决策智能化”等问题,为不同企业、不同阶段实现不同的经营目标。
请先 登录后发表评论 ~