工厂MES系统实施案例分享
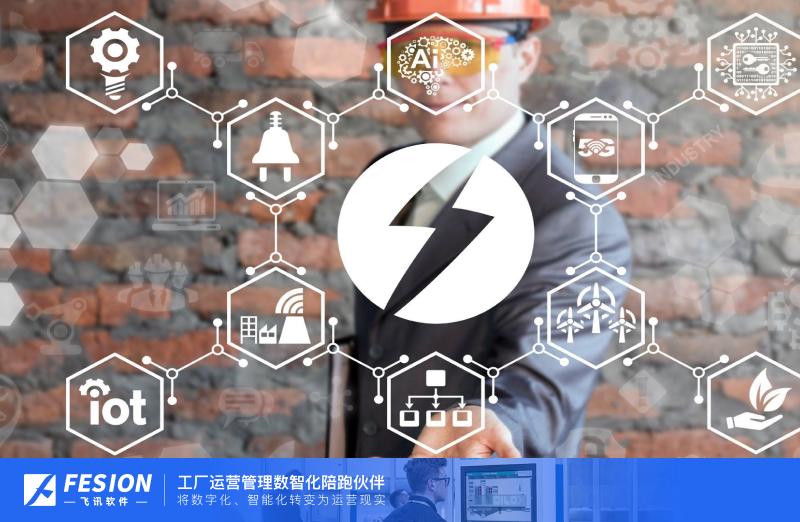
工厂MES系统实施案例分享
随着信息技术的不断发展,制造企业对于生产过程的管理需求也越来越高。MES(制造执行系统)作为数字化转型中的关键组成部分,为企业提供了全面的生产过程管理和优化手段。下面从多角度分享一个工厂MES系统的实施案例,以期为读者们提供一些实际操作上的参考。
1. 案例背景
某家汽车零部件制造企业决定引入MES系统,目的是提高生产效率、优化生产计划调度和减少生产成本。该企业拥有多条生产线,且生产过程中涉及多个环节和子系统的协同配合。因此,引入MES系统将有助于提升生产调度的准确性和响应速度,并实现全面自动化的生产数据收集与分析。
2. 实施目标
该企业的实施目标主要包括:
- 提高生产效率:通过MES系统的实时监控和反馈,及时发现生产过程中的异常情况,并采取相应措施进行调整,以避免生产线停机等不利因素。
- 优化生产计划调度:通过有效的订单管理和资源调度,确保原材料和设备的准时供应,避免生产计划延误和物料浪费。
- 减少生产成本:通过MES系统提供的数据分析和报告功能,对生产过程中的低效环节进行优化,降低能源消耗和人工成本。
3. 实施步骤
该企业的MES系统实施分为以下步骤:
- 需求分析:与供应商合作,详细了解企业现有的生产流程和问题所在,明确实施目标和需求。
- 系统设计:根据需求分析的结果,设计MES系统的功能模块和信息流程,明确数据采集与传输的方式。
- 软硬件配置:根据设计方案,采购相关硬件设备并进行安装、配置。同时,定制开发MES系统软件,并进行调试。
- 数据迁移与测试:将原有的生产数据迁移到MES系统中,进行数据清洗和格式转换。在此基础上,进行系统的功能测试和性能验证。
- 培训与上线:组织相关人员进行MES系统的培训和指导,确保他们掌握系统的操作和应用技巧。最后,正式上线运行。
4. 实施效果
经过MES系统的实施,该企业取得了显著的效果:
- 生产效率提升:MES系统实时监控和反馈的功能,使得生产异常情况能够及时发现和处理,大大减少了停机时间和废品率。
- 节约物料成本:通过MES系统的物料管理模块,可以更精细地控制物料的使用量和供应周期,从而降低物料库存和浪费。
- 精准生产计划:MES系统的生产调度功能,使得订单管理和资源调度更加准确和高效,避免了延误和过剩。
总结起来,该工厂的MES系统实施案例充分展示了MES系统在制造企业中的重要作用。通过引入MES系统,企业在生产过程管理、资源调度和成本控制等方面取得了实质性的改善。值得注意的是,MES系统的实施不仅仅是技术问题,还需要与企业的具体情况相结合,注重人员培训和组织变革,才能真正发挥其最大的效益。
飞讯软件成立于2006年,拥有自主研发低码开发平台。是一家集“营销、制造、采购”全链路数智化工厂定制方案商和服务商。产品服务:数字化车间、互联工厂和链主工厂。公司以MRO、ERP、MES、WMS、CRM、SRM等产品为基础,为客户提供数智化工厂整体方案规划和落地陪跑服务,服务范围覆盖珠三角和长三角地区。致力于帮助客户创立切合实际场景、可传承、可创新的数字化运营体系,解决“流程信息化、管理数字化和决策智能化”等问题,为不同企业、不同阶段实现不同的经营目标。
请先 登录后发表评论 ~