MES系统标准工艺应用案例分析
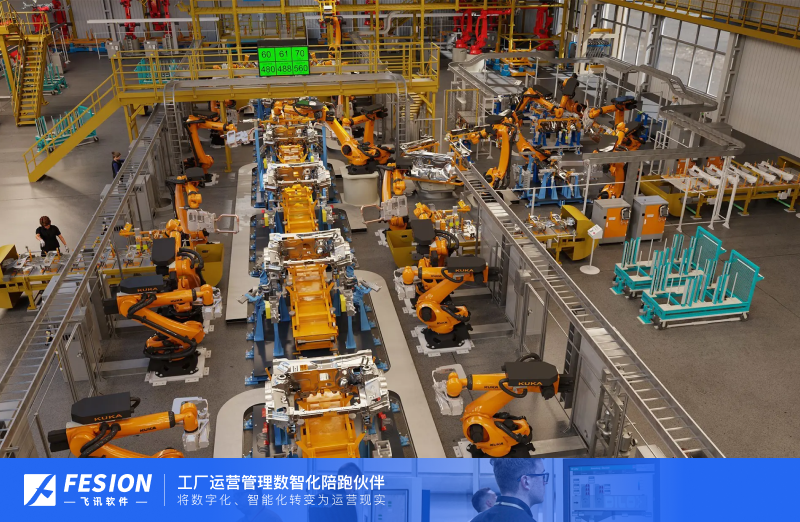
MES系统标准工艺应用案例分析
随着社会的发展和科技的进步,制造业的竞争日益激烈。要在这个竞争激烈的环境中获得优势,企业需要借助先进的管理技术和工具。MES系统(Manufacturing Execution System)作为一种集成的生产管理方案,通过实时跟踪和监控生产过程,提供了一种高效的生产管理方式。在本文中,我们将通过一个实际案例来分析MES系统在标准工艺应用中的优势和效果。
案例背景
某汽车制造公司为了提高生产效率和品质,决定引入MES系统来管理其标准工艺流程。该公司的生产过程非常复杂,涉及多个车间和工序。在引入MES系统之前,生产数据手动记录,无法及时准确地获取关键指标。因此,该公司决定通过MES系统实现工艺流程的标准化和自动化,并实时跟踪和监控生产过程。
系统实施与应用
在实施MES系统之前,该公司进行了详细的工艺流程分析,并与MES系统供应商合作,根据公司的实际情况进行定制开发。首先,他们将工艺流程和相关数据输入到MES系统中,包括工序顺序、工时、物料配送等信息。然后,他们对每个工序的操作人员进行培训,以确保他们熟悉MES系统的使用方法。最后,他们进行了一段时间的试运行和调试,以验证系统的稳定性和可靠性。
一旦MES系统正式投入使用,该公司立即感受到了其带来的诸多好处。首先,MES系统实现了标准化的工艺流程。每个工序的操作人员在执行工作时只需按照MES系统上显示的指导步骤进行操作,避免了操作过程中的错误和疏漏。其次,MES系统提供了实时的生产数据监控功能。生产数据可以通过仪表板和报表呈现,帮助管理人员及时了解生产状态,并进行相应的调整和决策。此外,MES系统还可以与其他企业管理系统集成,实现全面的信息共享。
效果分析
引入MES系统后,该公司的生产效率和品质得到了显著提升。首先,标准化的工艺流程减少了操作过程中的错误和疏漏,提高了产品的一致性和稳定性。其次,实时的生产数据监控使管理人员能够及时发现问题并采取行动,避免了延误和浪费。第三,MES系统的集成能力使得各个部门之间的协作更加紧密,信息共享更加便捷,提高了决策的准确性和时效性。
此外,MES系统还带来了其他一些附加效益。例如,通过自动化数据记录和报表生成,大大减少了人力资源的投入。同时,生产过程中的问题和异常可以得到及时反馈和处理,降低了不良品率和返工率。总的来说,MES系统在标准工艺应用中取得了显著的成效。
结论
通过上述案例分析我们可以看出,MES系统在标准工艺应用中具有重要的作用和优势。它能够帮助企业实现工艺流程的标准化和自动化,提高生产效率和品质。同时,它还能够提供实时的生产数据监控和管理功能,帮助企业及时发现问题并进行调整和决策。因此,对于追求高效生产管理的企业来说,引入MES系统是一个明智的选择。
需要注意的是,在引入MES系统时,企业需要进行详细的需求分析和实施计划制定,确保系统与企业的实际情况相匹配。此外,培训和技术支持也是成功实施和应用MES系统的重要环节。只有在系统完善、人员熟悉的情况下,才能充分发挥MES系统的优势和效果。
综上所述,MES系统作为一种先进的生产管理方案,在标准工艺应用中具有巨大的潜力和优势。通过合理的实施和应用,企业可以实现生产过程的高度精细化和优化,从而提升竞争力和市场份额。
飞讯软件成立于2006年,拥有自主研发低码开发平台。是一家集“营销、制造、采购”全链路数智化工厂定制方案商和服务商。产品服务:数字化车间、互联工厂和链主工厂。公司以MRO、ERP、MES、WMS、CRM、SRM等产品为基础,为客户提供数智化工厂整体方案规划和落地陪跑服务,服务范围覆盖珠三角和长三角地区。致力于帮助客户创立切合实际场景、可传承、可创新的数字化运营体系,解决“流程信息化、管理数字化和决策智能化”等问题,为不同企业、不同阶段实现不同的经营目标。
请先 登录后发表评论 ~