MES系统车间异常分析流程
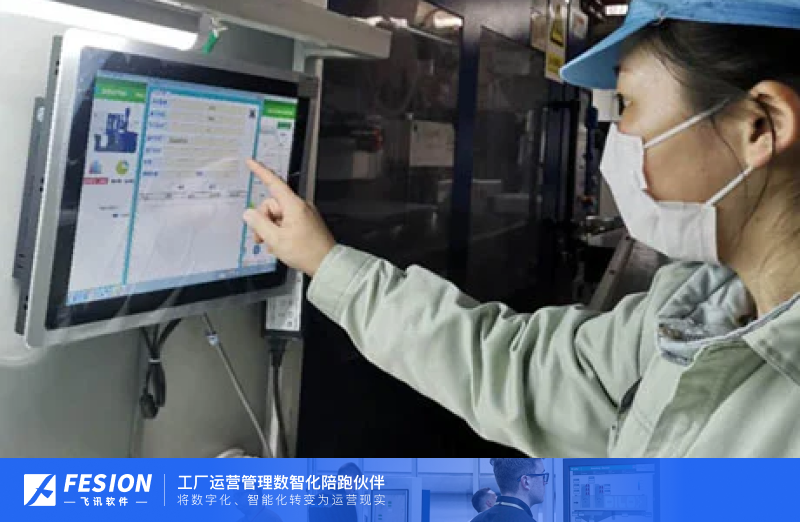
MES系统车间异常分析流程
随着制造业的发展,制造企业对于生产过程中的异常情况进行及时分析和解决变得越来越重要。而制造执行系统(MES)作为连接企业管理层与车间现场的桥梁,扮演着关键的角色。本文将介绍MES系统车间异常分析流程,探讨如何通过该流程提高生产效率和质量。
1. 数据采集与监控
在MES系统车间异常分析流程中,首先需要进行数据采集和监控。通过在车间设备和生产线上部署传感器、仪表等设备,实时采集相关数据,包括温度、压力、湿度、电流等参数。这些数据会被传输到MES系统的数据库中,并在监控界面上进行可视化展示。
2. 异常检测与识别
当数据采集完成后,MES系统会对数据进行异常检测和识别。系统会通过建立模型或设定规则,对采集到的数据进行实时分析。一旦出现异常情况,例如温度超过预设范围、设备产生故障等,系统将自动发出警报并记录异常事件的发生时间、位置和原因。
3. 异常报告与通知
一旦异常被系统检测到并识别出来,MES系统将生成异常报告并发送通知给相关人员。这些报告将包含详细的异常信息,例如异常类型、发生时间、设备编号等。通知可以通过手机短信、电子邮件或其他即时通讯工具发送给相应的管理人员和技术人员。
4. 异常分析与处理
接收到异常报告后,相关人员将进入异常分析与处理阶段。他们将仔细分析异常事件的原因,并采取相应的措施进行处理。这可能包括设备维修、更换零部件、调整工艺参数等。同时,异常事件的处理过程也会被记录下来,以便今后的参考和追溯。
5. 效果评估与改进
完成异常处理后,MES系统还会对整个流程进行效果评估和改进。系统会根据异常事件的处理时间、影响范围等指标,计算出异常管理的绩效。如果绩效低于预期,系统将提供相应的反馈和建议,以便改进车间异常分析流程,提高生产效率和质量。
结论
MES系统车间异常分析流程在制造企业中起着至关重要的作用。通过实时数据采集、异常检测和识别、异常报告与通知、异常分析与处理以及效果评估与改进,制造企业可以快速响应车间异常情况并采取相应措施。这不仅有助于提高生产效率和质量,还能减少停机时间和成本损失。因此,在实施MES系统时,合理设计和优化车间异常分析流程是非常重要的。
飞讯软件成立于2006年,拥有自主研发低码开发平台。是一家集“营销、制造、采购”全链路数智化工厂定制方案商和服务商。产品服务:数字化车间、互联工厂和链主工厂。公司以MRO、ERP、MES、WMS、CRM、SRM等产品为基础,为客户提供数智化工厂整体方案规划和落地陪跑服务,服务范围覆盖珠三角和长三角地区。致力于帮助客户创立切合实际场景、可传承、可创新的数字化运营体系,解决“流程信息化、管理数字化和决策智能化”等问题,为不同企业、不同阶段实现不同的经营目标。
请先 登录后发表评论 ~