工厂多系统集成改善质量控制
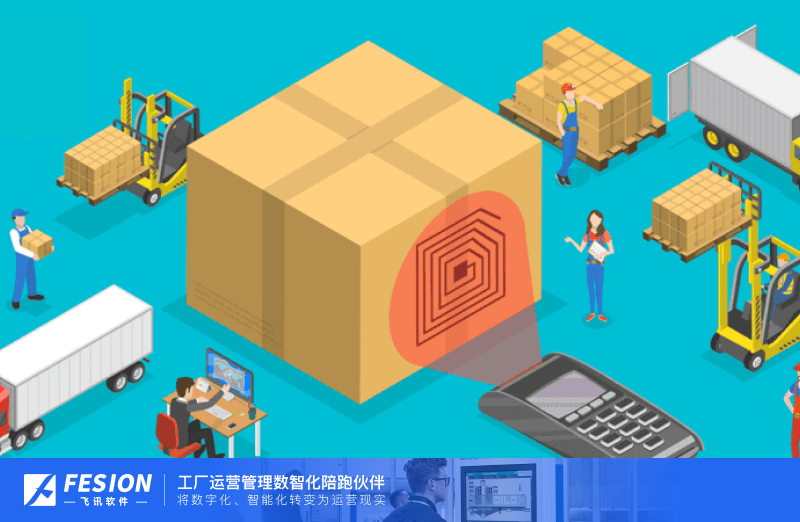
工厂多系统集成改善质量控制
随着科技的不断发展和工业生产的提升,现代工厂面临着越来越复杂的生产环境和质量控制难题。为了有效地解决这些问题,工厂多系统集成成为了一种被广泛采用的方式。本文将探讨如何通过工厂多系统集成来改善质量控制,提高生产效率和产品质量。
1.背景
在传统的生产环境中,工厂通常会使用多个独立的系统来监控和控制不同部分的生产过程。例如,一个工厂可能有单独的系统用于生产计划、库存管理、设备监控和质量控制等。然而,这些独立的系统之间缺乏有效的数据交流和协作,导致信息孤岛和生产管理的困难。
工厂多系统集成的目标是将这些独立的系统整合到一个统一的平台上,实现数据共享和系统协同。通过将不同系统的数据整合到一个集中的数据库中,并建立相应的数据交换和协作机制,工厂可以实现全面的信息化管理。
2.优势
工厂多系统集成带来了多个方面的优势,对于改善质量控制尤为重要。
2.1 实时数据监控
通过将各个生产环节的监控系统整合到一个平台上,工厂可以实现对所有数据的实时监控和分析。例如,通过集成设备监控系统,工厂可以及时获取设备的运行状态和故障信息,以便及时采取措施进行维修和保养。这样可以大大减少生产线停机时间,提高生产效率。
2.2 数据分析与预测
通过整合生产计划和库存管理系统,工厂可以更加准确地了解当前的生产状况和库存情况。基于这些数据,工厂可以进行深入的数据分析和预测,以便更好地规划生产计划和库存调配。这有助于减少库存积压和产能浪费,提高整体的资源利用效率。
2.3 故障预警和质量监控
通过集成质量控制系统和设备监控系统,工厂可以实现对生产过程中的故障和质量问题的实时监控和预警。例如,当某个环节出现异常时,系统可以及时发出警报并通知相关人员进行处理。这有助于及时发现和解决潜在的质量问题,提高产品的合格率。
3.实施步骤
要实现工厂多系统集成,需要经过以下几个步骤:
3.1 系统评估
首先,工厂需要对现有的系统进行全面的评估,了解各个系统的功能和数据结构。同时,也需要评估工厂的信息化水平和技术基础,以确定集成方案的可行性和复杂度。
3.2 数据整合
在评估的基础上,工厂需要制定数据整合方案,确定数据交换和共享的方式。这包括建立数据接口、数据格式标准化和数据传输协议等。同时,还需要进行数据清洗和转换,以确保数据的一致性和准确性。
3.3 系统集成
在数据整合的基础上,工厂需要进行系统集成。这包括开发集成平台和相应的系统接口,实现不同系统之间的数据交换和协同。同时,也需要进行系统测试和调试,确保集成后的系统正常运行。
3.4 培训和运维
完成系统集成后,工厂需要进行相关人员的培训,使其熟悉集成平台的操作和管理。同时,也需要建立定期的系统维护和更新机制,及时修复漏洞和优化系统性能。
4.案例实践
以下是一个工厂多系统集成改善质量控制的案例实践:
某汽车制造厂通过集成生产计划、设备监控和质量控制等系统,实现了全面的生产管理和质量监控。通过集成后的系统,他们能够实时监控生产线上每个环节的生产情况和设备状态,并及时发现和解决潜在的故障和质量问题。这使得他们的产品质量得到了显著提升,客户满意度也大幅提高。
总结
工厂多系统集成是改善质量控制和提高生产效率的重要手段。通过整合不同系统的数据和功能,工厂可以实现实时监控、数据分析和质量预警等功能,从而更好地应对复杂的生产环境和提升产品质量。然而,实施多系统集成需要进行全面的评估和规划,并且需要培训相关人员和建立有效的运维机制。只有在科学合理的方案和有效的执行下,工厂多系统集成才能发挥最大的作用。
飞讯软件成立于2006年,拥有自主研发低码开发平台。是一家集“营销、制造、采购”全链路数智化工厂定制方案商和服务商。产品服务:数字化车间、互联工厂和链主工厂。公司以MRO、ERP、MES、WMS、CRM、SRM等产品为基础,为客户提供数智化工厂整体方案规划和落地陪跑服务,服务范围覆盖珠三角和长三角地区。致力于帮助客户创立切合实际场景、可传承、可创新的数字化运营体系,解决“流程信息化、管理数字化和决策智能化”等问题,为不同企业、不同阶段实现不同的经营目标。
请先 登录后发表评论 ~